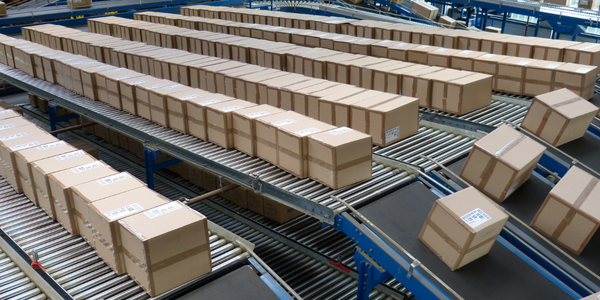
- Automation & Control - Supervisory Control & Data Acquisition (SCADA)
- Packaging
- Discrete Manufacturing
- Process Control & Optimization
KHS develops and produces machines and equipment for filling and packaging in the drinks industry. Because drinks manufacturing, filling and packaging consist of a number of highly complex processes, the user-friendly and intuitive operation of equipment is increasingly gaining in significance. In order to design these processes as simple as possible for the user, KHS decided to introduce a uniform, transparent and standardized solution to the company. The HMI interface should meet the requirement for people with different qualifications and enable them to work on a standard platform.
KHS decided to use Zenon from COPA-DATA for the implementation of the new ClearLine HMI. The Zenon HMI/SCADA platform offers precisely what we need for our machines and production lines. The zenon software has well-developed graphical display possibilities and numerous HMI elements already included as standard. Software Components - Zenon: the HMI/SCADA software from COPA-DATA - Everywhere App
Case Study missing?
Start adding your own!
Register with your work email and create a new case study profile for your business.
Related Case Studies.
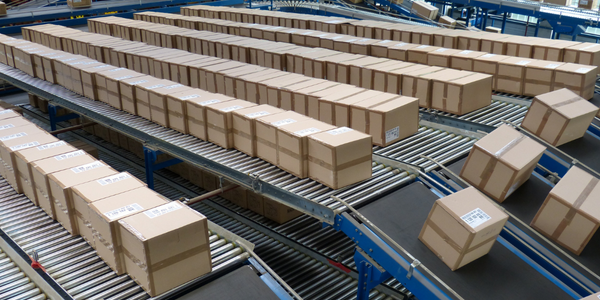
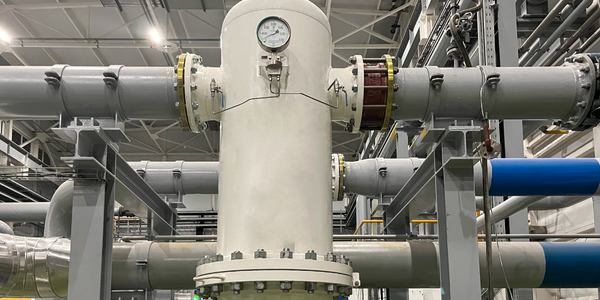
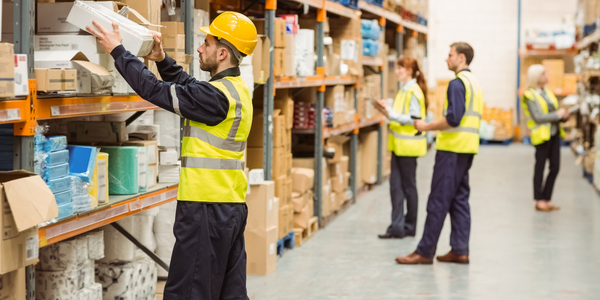
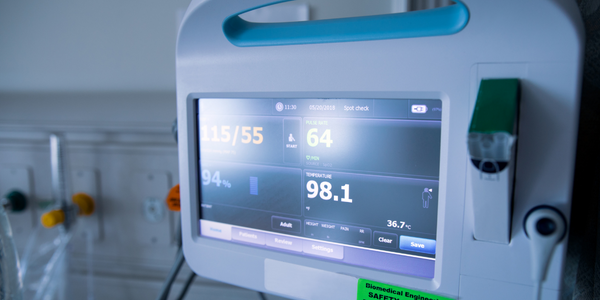
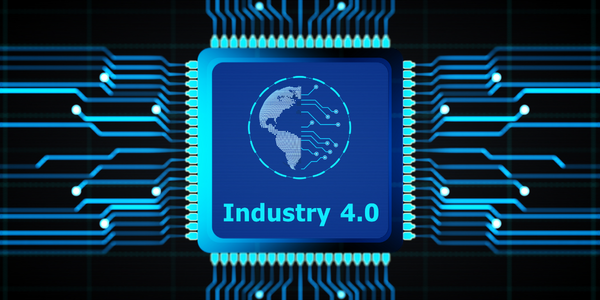
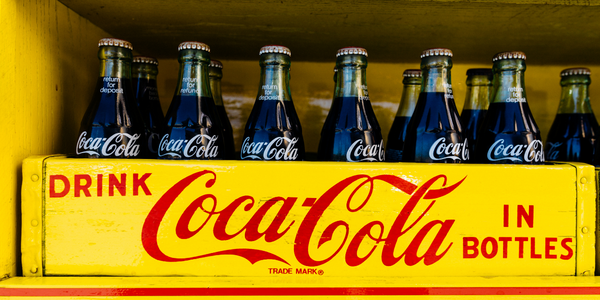