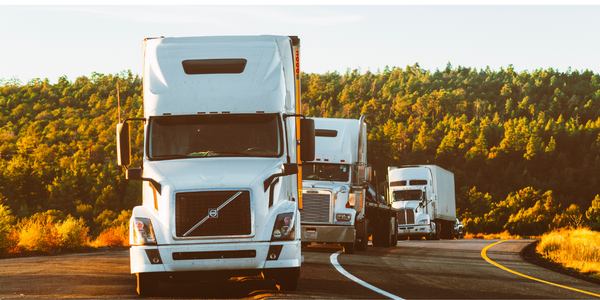
- Analytics & Modeling - Digital Twin / Simulation
- Analytics & Modeling - Virtual & Augmented Reality Software
- Automotive
- Discrete Manufacturing
- Digital Thread
- Hardware Design & Engineering Services
Volvo Trucks
Global truck manufacturer
In today’s rapidly changing market, customization has become the new normal. This presents new quality assurance challenges as product complexity and unique configurations increase in volume and rate of change.
Volvo’s engines are very sophisticated with 4,500 different engine information variants for just one plant and for 13,000 variants for the full plant for referencing.
Training new operators on the complex inspection procedures takes five weeks, which adds to the overall cost of quality.
Utilizing PTC not only for its leading Vuforia enterprise Augmented Reality suite of capabilities, but also for its end-to-end solution for creating and scaling a digital thread.
Utilizing the ThingWorx Industrial Internet of Things platform, engineering updates from Creo engine computer- aided design (CAD) iterations, downstream Windchill product lifecycle management (PLM) and manufacturing operations technology
Case Study missing?
Start adding your own!
Register with your work email and create a new case study profile for your business.
Related Case Studies.
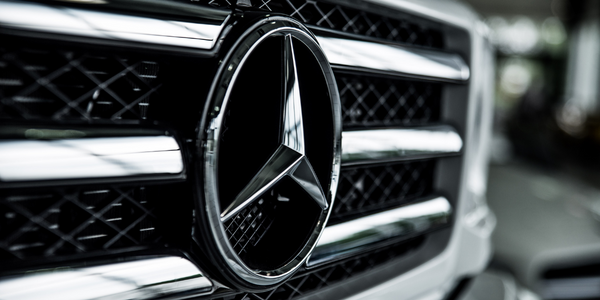
