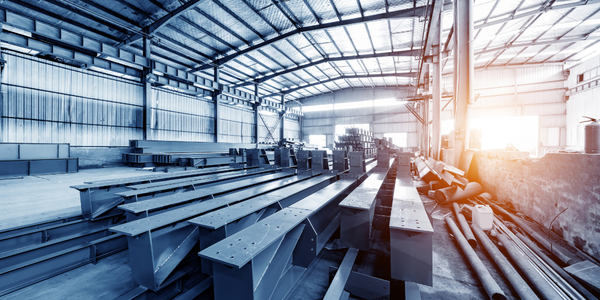
- Functional Applications - Fleet Management Systems (FMS)
- Equipment & Machinery
- Discrete Manufacturing
- Fleet Management
ThyssenKrupp Steel Europe found itself in the position of needing to replace, step by step, the models it had programmed itself to manage the production of various grades of steel with a solution equipped to face the demands of the future. The solution had to be easy to integrate and designed to be rolled out step by step. ThyssenKrupp Steel Europe uses its automation systems to manage the whole production process at its company steel plants. This is done using clever algorithms that map the functional relationships across all stages of the steel production process. However, there are still a host of other changeable factors that influence the quality of the product obtained, and these also need to be factored in in the form of rules or formulae. What ThyssenKrupp Steel Europe was looking for was a suitable piece of software to fulfill this rule-based management function.
ThyssenKrupp opted for Bosch Software Innovations’ Visual Rules – Business Rules Management (BRM) system. In its modeling of the rules governing the formula for the steel, the software demonstrates agility and transparency – two things that are critical to the company’s success. Modeling the rules using Visual Rules will provide ThyssenKrupp with an agile solution for the production of various grades of steel. Implementation is underway for all of the rule- and formula-based knowledge that will serve to manage processes and aid decision making in the production process. Thanks to the transparency and easy modification of the rules models, any future changes to production requirements (production method, special treatments, special conditions to be respected, etc.) will be easily accommodated and the path to a steel product tailored to customers’ altered needs greatly expedited. In the case of a new steel formula for a new product within an existing product family, the production specifications will be generated automatically – guaranteeing a high level of consistency in the production techniques employed.
Case Study missing?
Start adding your own!
Register with your work email and create a new case study profile for your business.
Related Case Studies.


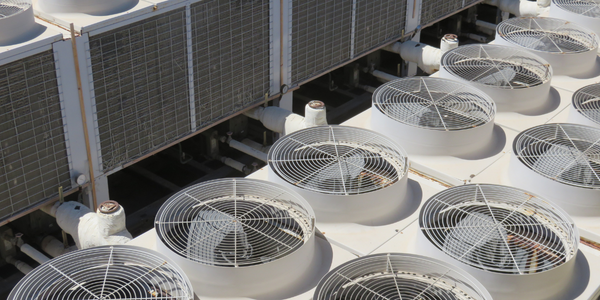


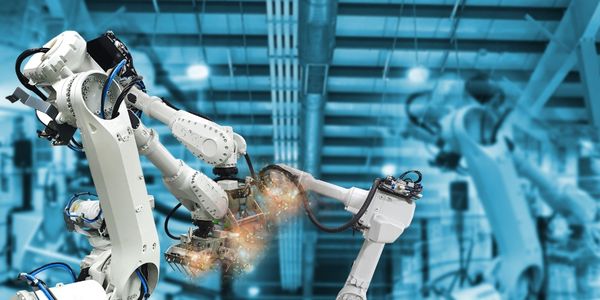