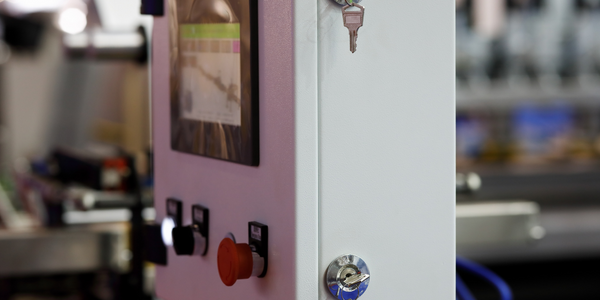
- Automation & Control - Human Machine Interface (HMI)
- Automation & Control - Supervisory Control & Data Acquisition (SCADA)
- Functional Applications - Remote Monitoring & Control Systems
- Utilities
- Business Operation
- Remote Asset Management
Tacoma Power, located in Tacoma, WA, serves 160,000 electric utility customers with nine hydro facilities on four rivers. The company’s generation automation team, consisting of three engineers and one engineering technician, is responsible for the integration, modernization. With a small staff responsible for overseeing a number of different environments, the company was looking to implement its HMI/SCADA system in a virtual environment for automation and control in order to optimize operations and reduce costs.
To make the business case for virtualization, Tacoma Power management reviewed the costs and benefits. The justification was clear, as the company proved a small upfront investment with savings in the long run through speed, uptime, and significant risk reduction. With approval and support to proceed at the executive level, Tacoma Power added virtualization to its regular budget for system life-cycle replacement, leveraged an IT consultant for expert advice, and planned its deployment process.
The company deployed a multi-phase virtualization project with GE Digital’s HMI/SCADA iFIX using Microsoft Hyper-V across its hydroelectric and fish hatchery facilities. In addition to visualization and control, Tacoma Power also implemented iFIX for trending, troubleshooting, and continuous optimization. Data collection and management is critical for regulatory reporting as well as day-to-day operations. And, giving operators access to HMI screens from remote devices was important for speeding response to hatchery related alarms.
Case Study missing?
Start adding your own!
Register with your work email and create a new case study profile for your business.
Related Case Studies.



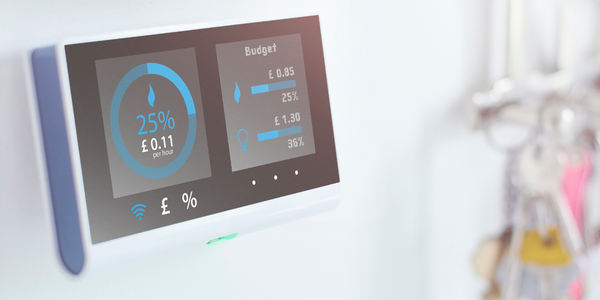

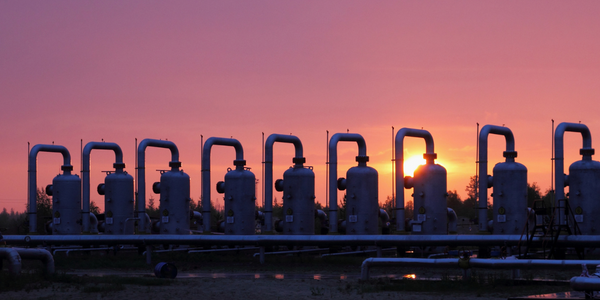