Quality compressed air for high-tech products
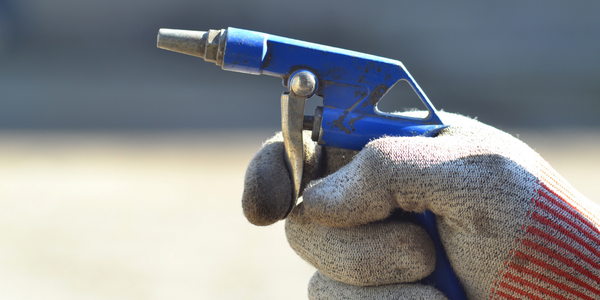
- Functional Applications - Remote Monitoring & Control Systems
- Sensors - Pressure Sensors
- Maintenance
- Predictive Maintenance
When it came to modernisation of the existing compressed air station, the company’s management decided to opt for a compressed air contracting arrangement to ensure that the compressed air supply would always meet the latest technical standards and be capable of taking advantage of the benefits that Industry 4.0 has to offer – and not least due to the frequent fluctuations in demand in the automotive supplier industry. In this operator model, the compressed air station itself remains the property of the air system provider, whilst the customer simply uses the compressed air as needed, just like power from an electrical socket, paying only for the volume of compressed air actually used – and always at the same fixed rate. From an accounting perspective, this effectively turns fixed costs into variable costs. At Scholz, the new station was installed in a space-saving container on the roof of the company building.
Following a detailed compressed air audit to identify the company’s exact compressed air needs, Scholz’s compressed air station was designed to incorporate the very latest technology, including all of the features that today’s advanced stations should offer. Of course, first and foremost, this includes outstanding reliability, quality and efficiency, as well as impressive energy savings. In addition, ease of maintenance together with networking and integrated control features consistent with the Industry 4.0 environment also play a key role, not least in laying the foundation for predictive maintenance. A safety concept was also devised. The data gathered during the analysis were input into the new system's controller – a SIGMA AIR MANAGER 4.0 (SAM 4.0) in this case – and therefore provide the foundation for highly-efficient operation of the entire system. Since the compressors and compressed air treatment components are equipped with integrated industrial PC technology, they are able to forward their data to a master controller. This master controller monitors all components, as well as the environmental and production conditions. is also able to precisely adapt compressed air production to match the company’s actual compressed air requirement. Furthermore, amongst many other key benefits, the SAM 2 optimises pressure values, automatically adjusts compressor system air delivery to accommodate fluctuating air demand and optimises system efficiency through constant analysis of the relationship between control losses, switching losses and pressure flexibility. This advanced controller also enables the compressed air station to benefit from future services, such as predictive maintenance. The controller also allows remote diagnostics capability. If requested by the customer, this option means that performance data are constantly sent to a data centre operated by the compressed air system provider for monitoring. The master controller independently analyses the situation at all times and, if appropriate, sends a message to the service team, or directly to the local installation technician or the central data centre. The air system provider’s central data centre then acts as the dispatching point for all further activities – worldwide.
Case Study missing?
Start adding your own!
Register with your work email and create a new case study profile for your business.
Related Case Studies.

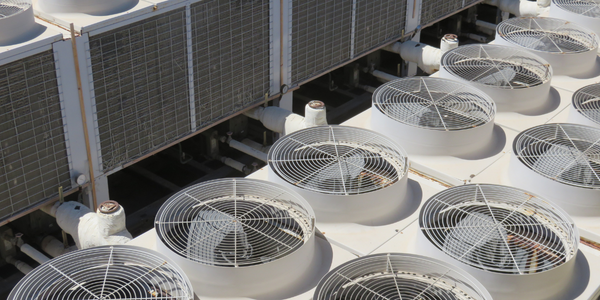
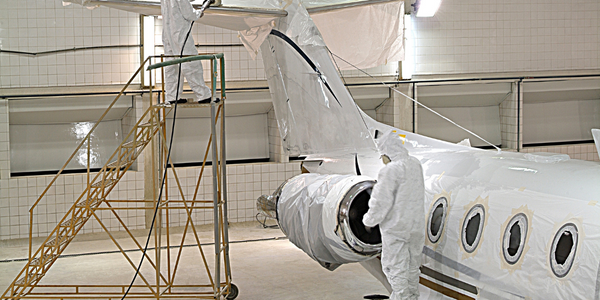
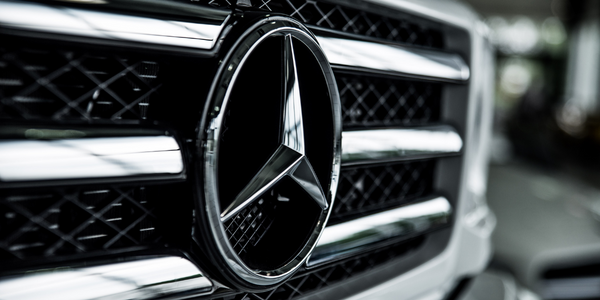
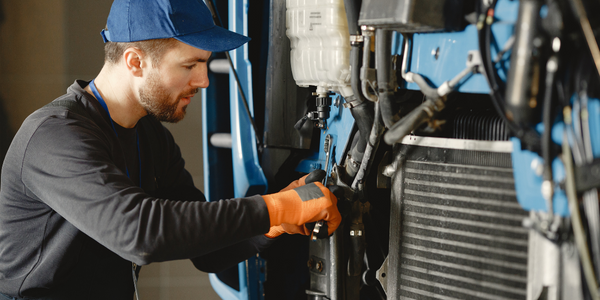