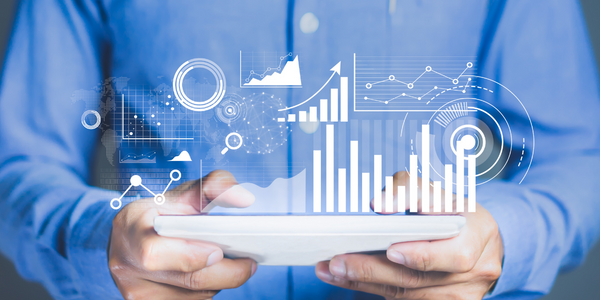
Technology Category
- Analytics & Modeling - Real Time Analytics
Applicable Industries
- Aerospace
- Automotive
Applicable Functions
- Maintenance
- Quality Assurance
Use Cases
- Asset Lifecycle Management
- Real-Time Location System (RTLS)
Services
- Testing & Certification
- Training
The Customer
Wiscon Products
About The Customer
Wiscon Products is a precision parts manufacturer based in Racine, WI. The company produces quality parts for a variety of industries, including aerospace, medical, energy, automotive, construction, and power. In 2018, Wiscon began utilizing MachineMetrics at its facility to align with its core goals of process improvement, reduced downtime, and increased equipment utilization. The company wanted to better serve its growing client base and gain complete control of its data.
The Challenge
Wiscon Products, a precision parts manufacturer, faced a significant challenge in data accuracy. The company's manual data collection methods were outdated and inefficient, often resulting in data that was several days to a week old by the time it was reviewed. This lack of real-time data made it difficult for the company to make informed decisions and implement improvements. Wiscon also struggled with gaining insight into production downtime, cycle time, and equipment utilization. The company had questions about how often spindles were turning and how many parts were being produced. Despite investing over $16 million on equipment, Wiscon was always running at capacity, and there were gaps and delays in the data, leading to a lack of visibility and an inability to respond to issues quickly.
The Solution
To address these challenges, Wiscon deployed MachineMetrics at its facility. This resulted in significant efficiency gains across production and provided teams with complete visualization of real-time data. The company was able to shift from a reactive to a proactive approach, driving critical improvements in planning and scheduling processes. MachineMetrics provided critical benchmarking information that helped management understand the value of categorized downtime and accurate production performance. This guided the development of data-driven improvements and empowered actionable decision-making. The platform also integrated quickly with Wiscon’s existing ERP and QMS systems, enabling operators to focus on quality instead of administration and data entry. The extensibility of existing systems gave Wiscon a considerable advantage in using real-time data to improve operator efficiency.
Operational Impact
Quantitative Benefit
Case Study missing?
Start adding your own!
Register with your work email and create a new case study profile for your business.
Related Case Studies.
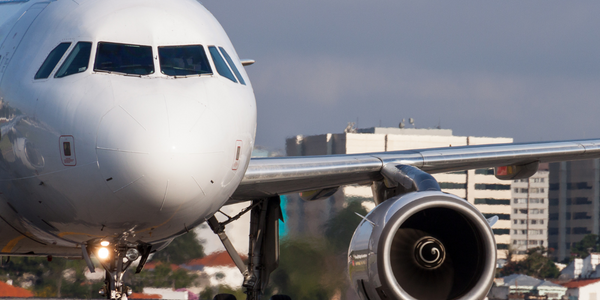
Case Study
Airbus Soars with Wearable Technology
Building an Airbus aircraft involves complex manufacturing processes consisting of thousands of moving parts. Speed and accuracy are critical to business and competitive advantage. Improvements in both would have high impact on Airbus’ bottom line. Airbus wanted to help operators reduce the complexity of assembling cabin seats and decrease the time required to complete this task.
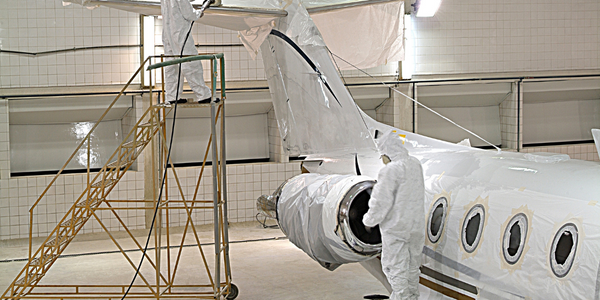
Case Study
Aircraft Predictive Maintenance and Workflow Optimization
First, aircraft manufacturer have trouble monitoring the health of aircraft systems with health prognostics and deliver predictive maintenance insights. Second, aircraft manufacturer wants a solution that can provide an in-context advisory and align job assignments to match technician experience and expertise.
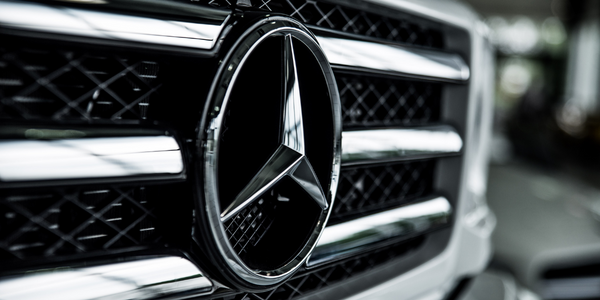
Case Study
Integral Plant Maintenance
Mercedes-Benz and his partner GAZ chose Siemens to be its maintenance partner at a new engine plant in Yaroslavl, Russia. The new plant offers a capacity to manufacture diesel engines for the Russian market, for locally produced Sprinter Classic. In addition to engines for the local market, the Yaroslavl plant will also produce spare parts. Mercedes-Benz Russia and his partner needed a service partner in order to ensure the operation of these lines in a maintenance partnership arrangement. The challenges included coordinating the entire maintenance management operation, in particular inspections, corrective and predictive maintenance activities, and the optimizing spare parts management. Siemens developed a customized maintenance solution that includes all electronic and mechanical maintenance activities (Integral Plant Maintenance).
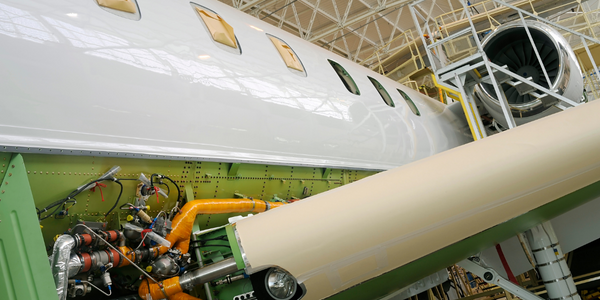
Case Study
Aerospace & Defense Case Study Airbus
For the development of its new wide-body aircraft, Airbus needed to ensure quality and consistency across all internal and external stakeholders. Airbus had many challenges including a very aggressive development schedule and the need to ramp up production quickly to satisfy their delivery commitments. The lack of communication extended design time and introduced errors that drove up costs.