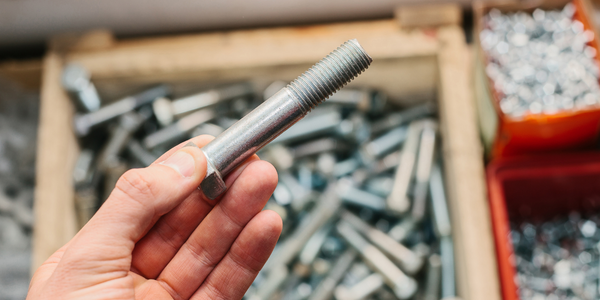
- Functional Applications - Manufacturing Execution Systems (MES)
- Equipment & Machinery
- Discrete Manufacturing
- Process Control & Optimization
Given the vast array of manufacturing fastening tools and assembly line device products available on the market, it can become overwhelming to identify which products you should purchase; as recommended by consultants or the tool suppliers themselves. Is it worth spending ‘extra money’ because of claims of added features and benefits? The question is, what is it you really-need to accomplish the task? What if you could purchase the most basic or cost-effective tool ‘needed’ for the job, with saved money in hand to put towards the over-all manufacturing execution system (MES) solution you really need? This is proven to be so, and fastening tool processes are a prime target application for manufacturers to improve their existing manufacturing operations (upgrade), or for new project specification; please consider the following.
The MES or MOM system is central to deciphering and creating actions from all the manufacturing data being received (monitored), in order to act (control and alert) in real time accordingly, and in order to output the granularity of manufacturing, or Andon data, essential to maximizing quality and production output (OEE) and optimizing process step cycle time. Therefore as proven and recommended, consider the MES system to be the primary focus in your plans to improve manufacturing processes, and as the starting point for your new project; because the tools and devices you connect to the network are secondary in the over-all manufacturing optimization scope of things; the fastening tools will serve their basic purpose to accept inputs and transmit outputs to the MES, the vital data needed for the manufacturing execution system to verify and command processes. The elimination of the need to spend additional money for unrequired features on fastening tools is notable, since so long as the fastening tool has a built in transducer it can be paired quite effectively via open protocol to communicate with the MES to ensure error-proofing in fastening operations is never compromised.
Case Study missing?
Start adding your own!
Register with your work email and create a new case study profile for your business.
Related Case Studies.


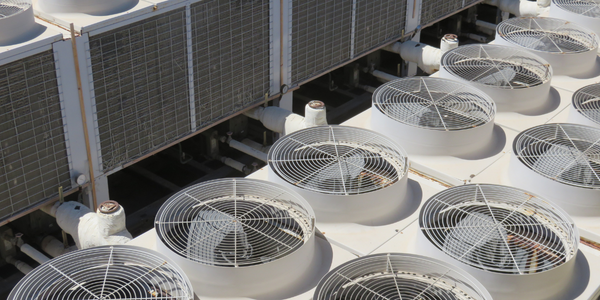


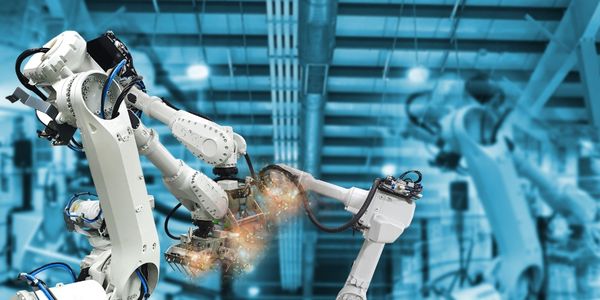