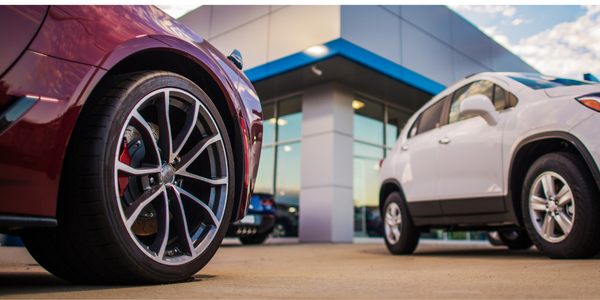
- Analytics & Modeling - Computer Vision Software
- Automotive
- Discrete Manufacturing
- Computer Vision
- System Integration
IBG Automation GmbH
Automation solutions provider.
Using manual assembly methods to mount wheels onto cars in continuous operation is extremely costly for automotive manufacturers. This is mainly because several assembly workers are required to perform the work.
Two six-axis industrial robots—one located on each side of a car body—gather wheel bolts and rims from their supply stations and screw them onto the car. The robots are synchronized with the conveyor and follow the car’s movement during assembly. Attached to each robot is specialized lighting with polarized and infrared filters. A Matrox Iris GT smart camera is also attached to each robot. The smart camera locates the rim’s centre point and calculates its position (x, y), rotation (Rz) of the bolt circle, and distance to the camera (z) in calibrated coordinates. Before these coordinates are given to the robot, the smart camera checks to see whether the rim design that it has located matches the rim that is expected to be given by the PLC. This last test prevents the wrong rim design from being mounted on the vehicle. Thirteen different wheel combinations—seven rim designs and four types of lacquer (white, silver, anthracite, and black)—are identified. The entire automated wheel assembly process has a cycle time of only 54 seconds.
The image processing system is based upon the Matrox Iris GT smart camera. The application was developed with Matrox Design Assistant, an integrated development environment (IDE) that is bundled with the camera.
Case Study missing?
Start adding your own!
Register with your work email and create a new case study profile for your business.
Related Case Studies.
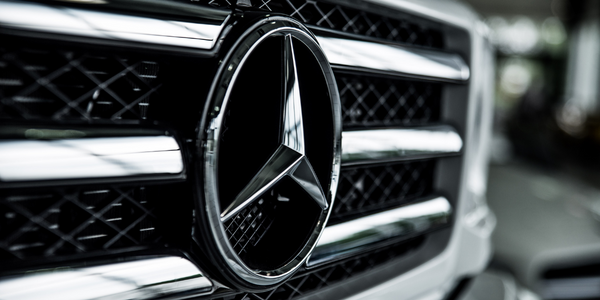
