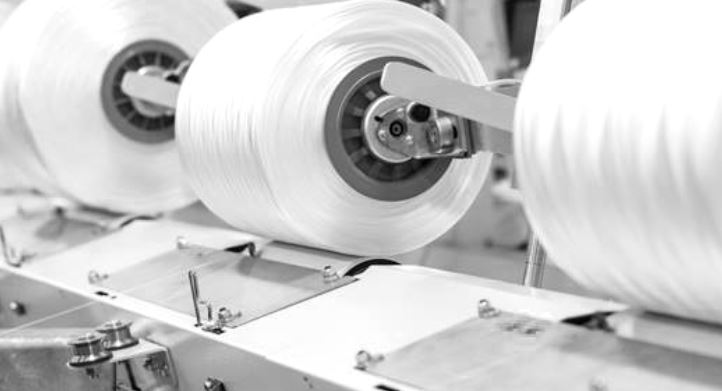
Technology Category
- Functional Applications - Computerized Maintenance Management Systems (CMMS)
- Functional Applications - Manufacturing Execution Systems (MES)
Applicable Industries
- Electronics
- Equipment & Machinery
Applicable Functions
- Maintenance
- Procurement
Use Cases
- Additive Manufacturing
- Digital Thread
Services
- Hardware Design & Engineering Services
- System Integration
The Customer
Service Thread
About The Customer
Service Thread is a leading American manufacturer of commercial thread and yarn. The company operates a large factory in Laurinburg, NC, which houses over 3,000 spindles across 115,000ft2 of floor space and 24 different machine types. Service Thread is committed to optimizing its operations and was seeking a solution to effectively monitor and analyze its factory performance. The company's goal was to increase efficiencies, reduce costs, and fully optimize their production.
The Challenge
Service Thread, a leading American manufacturer of commercial thread and yarn, faced significant challenges in monitoring and analyzing their factory performance. With over 3,000 spindles across 115,000ft2 of floor space and 24 different machine types, the company struggled to effectively determine the actual utilization percentage of their factory. The traditional method of frequent and selective in-person inspections of the machines was not only time-consuming but also lacked accuracy. The company was in dire need of a solution that could provide real-time, accurate data on machine utilization to help them make informed business decisions and optimize their operations.
The Solution
Service Thread partnered with Logical Advantage to implement an IoT-based monitoring solution using the Particle Photon. This hardware solution was designed to gather data from the machines’ existing sensors, capable of monitoring 16 spindles simultaneously. The collected data was then transmitted through the Particle Cloud and onto Microsoft’s Azure IoT Hub using Wi-Fi. Logical Advantage also developed a mobile app for spindle sensor provisioning. This IoT solution provided Service Thread with real-time data on machine utilization, enabling them to identify inefficiencies and make informed decisions on equipment purchases, labor allocation, and overall operational optimization.
Operational Impact
Quantitative Benefit
Case Study missing?
Start adding your own!
Register with your work email and create a new case study profile for your business.
Related Case Studies.

Case Study
Smart Water Filtration Systems
Before working with Ayla Networks, Ozner was already using cloud connectivity to identify and solve water-filtration system malfunctions as well as to monitor filter cartridges for replacements.But, in June 2015, Ozner executives talked with Ayla about how the company might further improve its water systems with IoT technology. They liked what they heard from Ayla, but the executives needed to be sure that Ayla’s Agile IoT Platform provided the security and reliability Ozner required.

Case Study
IoT enabled Fleet Management with MindSphere
In view of growing competition, Gämmerler had a strong need to remain competitive via process optimization, reliability and gentle handling of printed products, even at highest press speeds. In addition, a digitalization initiative also included developing a key differentiation via data-driven services offers.

Case Study
Remote Temperature Monitoring of Perishable Goods Saves Money
RMONI was facing temperature monitoring challenges in a cold chain business. A cold chain must be established and maintained to ensure goods have been properly refrigerated during every step of the process, making temperature monitoring a critical business function. Manual registration practice can be very costly, labor intensive and prone to mistakes.
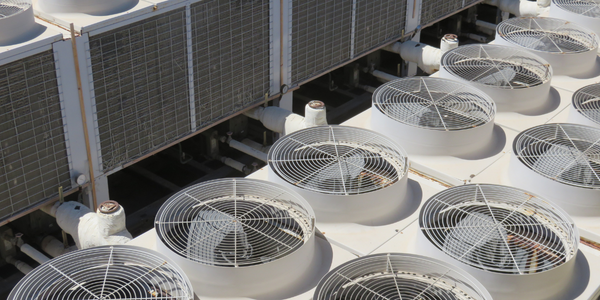
Case Study
Predictive Maintenance for Industrial Chillers
For global leaders in the industrial chiller manufacturing, reliability of the entire production process is of the utmost importance. Chillers are refrigeration systems that produce ice water to provide cooling for a process or industrial application. One of those leaders sought a way to respond to asset performance issues, even before they occur. The intelligence to guarantee maximum reliability of cooling devices is embedded (pre-alarming). A pre-alarming phase means that the cooling device still works, but symptoms may appear, telling manufacturers that a failure is likely to occur in the near future. Chillers who are not internet connected at that moment, provide little insight in this pre-alarming phase.

Case Study
Premium Appliance Producer Innovates with Internet of Everything
Sub-Zero faced the largest product launch in the company’s history:It wanted to launch 60 new products as scheduled while simultaneously opening a new “greenfield” production facility, yet still adhering to stringent quality requirements and manage issues from new supply-chain partners. A the same time, it wanted to increase staff productivity time and collaboration while reducing travel and costs.