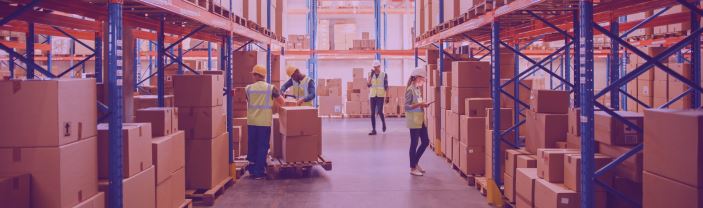
Technology Category
- Analytics & Modeling - Machine Learning
- Functional Applications - Product Data Management Systems
Applicable Industries
- E-Commerce
- Equipment & Machinery
Applicable Functions
- Procurement
- Sales & Marketing
Use Cases
- Augmented Reality
- Inventory Management
Services
- System Integration
- Testing & Certification
The Customer
IDI Independent Distributors Inc.
About The Customer
IDI Independent Distributors Inc. is a Canadian-owned business that serves the industrial and safety industries. It consists of approximately 104 shareholder owners, over 360 branches, 2,500 employees, almost $200 million in inventory, over $1.3 billion in gross annual revenues, and $900 million in purchasing power. IDI’s mission is to advance the success of its independent corporate shareholders and to work in harmony with them toward the continuation of that success in a free enterprise system. This commitment to advancement and collaboration led the group to explore a Product Information Management (PIM) system for its members.
The Challenge
IDI Independent Distributors Inc., a Canadian-owned business serving the industrial and safety industries, faced a challenge in providing its members with high-quality, enriched product information. The company recognized that its members needed a central repository for data to deliver consistent and trusted product information across various channels. However, smaller individual distributors lacked the resources to deploy a full Product Information Management (PIM) solution independently. IDI decided to invest strategically in a data management solution to help its members compete effectively in the digital marketplace with high-quality content. The goal was to build a vast repository of rich product content and digital assets to aid its members in growing their business across channels.
The Solution
IDI opted for the market-leading EnterWorks Member PIM solution. This solution allowed IDI members to subscribe to content from the master catalog and customize it to their needs. The program leveraged IDI’s product content while also enabling each member to tailor the content to their unique marketing and selling model. All product information and content could be managed under one platform, with a robust set of workflow tools for internal and external collaboration. The PIM system also featured a supplier portal that allowed suppliers to directly import product information. Members could then select the products they wanted, customize the information, and publish the data to their e-commerce websites and catalogs as needed. IDI planned to connect the PIM with hundreds of suppliers to keep the IDI product catalog dynamically updated and validated with the most current information.
Operational Impact
Case Study missing?
Start adding your own!
Register with your work email and create a new case study profile for your business.
Related Case Studies.

Case Study
Smart Water Filtration Systems
Before working with Ayla Networks, Ozner was already using cloud connectivity to identify and solve water-filtration system malfunctions as well as to monitor filter cartridges for replacements.But, in June 2015, Ozner executives talked with Ayla about how the company might further improve its water systems with IoT technology. They liked what they heard from Ayla, but the executives needed to be sure that Ayla’s Agile IoT Platform provided the security and reliability Ozner required.

Case Study
IoT enabled Fleet Management with MindSphere
In view of growing competition, Gämmerler had a strong need to remain competitive via process optimization, reliability and gentle handling of printed products, even at highest press speeds. In addition, a digitalization initiative also included developing a key differentiation via data-driven services offers.
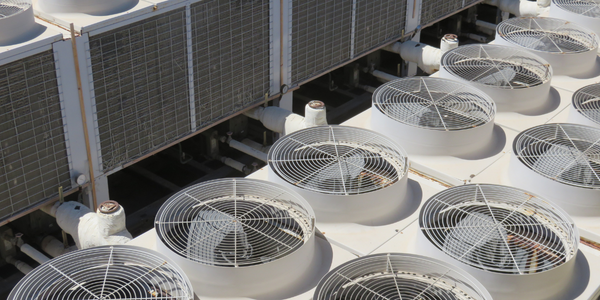
Case Study
Predictive Maintenance for Industrial Chillers
For global leaders in the industrial chiller manufacturing, reliability of the entire production process is of the utmost importance. Chillers are refrigeration systems that produce ice water to provide cooling for a process or industrial application. One of those leaders sought a way to respond to asset performance issues, even before they occur. The intelligence to guarantee maximum reliability of cooling devices is embedded (pre-alarming). A pre-alarming phase means that the cooling device still works, but symptoms may appear, telling manufacturers that a failure is likely to occur in the near future. Chillers who are not internet connected at that moment, provide little insight in this pre-alarming phase.

Case Study
Premium Appliance Producer Innovates with Internet of Everything
Sub-Zero faced the largest product launch in the company’s history:It wanted to launch 60 new products as scheduled while simultaneously opening a new “greenfield” production facility, yet still adhering to stringent quality requirements and manage issues from new supply-chain partners. A the same time, it wanted to increase staff productivity time and collaboration while reducing travel and costs.

Case Study
Integration of PLC with IoT for Bosch Rexroth
The application arises from the need to monitor and anticipate the problems of one or more machines managed by a PLC. These problems, often resulting from the accumulation over time of small discrepancies, require, when they occur, ex post technical operations maintenance.
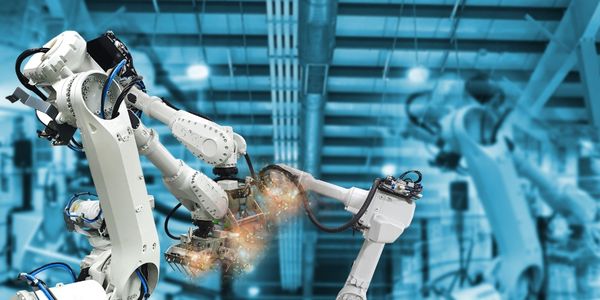
Case Study
Robot Saves Money and Time for US Custom Molding Company
Injection Technology (Itech) is a custom molder for a variety of clients that require precision plastic parts for such products as electric meter covers, dental appliance cases and spools. With 95 employees operating 23 molding machines in a 30,000 square foot plant, Itech wanted to reduce man hours and increase efficiency.