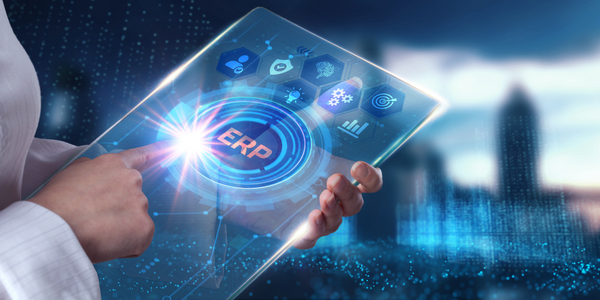
Technology Category
- Analytics & Modeling - Process Analytics
- Functional Applications - Enterprise Resource Planning Systems (ERP)
Applicable Industries
- Cement
- Oil & Gas
Applicable Functions
- Facility Management
- Procurement
Use Cases
- Construction Management
- Rapid Prototyping
Services
- System Integration
The Customer
Heerema Fabrication Group (HFG)
About The Customer
Heerema Fabrication Group (HFG) is part of the Heerema Group, a leading company in the offshore oil & gas and energy, engineering and construction industry. The Heerema Group designs, constructs, transports, installs and removes offshore facilities for the global oil & gas and energy industry. Over the years, Heerema has become a significant international player in the offshore construction industry. The Heerema Group consists of two divisions: the Heerema Fabrication Group (HFG) and Heerema Marine Contractors (HMC). HFG specializes in the engineering and fabrication of large and complex structures, while HMC transports, installs and removes all types of offshore facilities. HFG has three yards around the North Sea, two in the Netherlands (Zwijndrecht and Vlissingen) and one in Hartlepool in the UK. In 2006, HFG acquired an engineering company in the US. HFG has more than 800 employees worldwide and over 2,500 subcontractors.
The Challenge
Heerema Fabrication Group (HFG), a leading company in the offshore oil & gas and energy, engineering and construction industry, was facing a significant challenge. For over a decade, HFG had been using custom-built software for its primary business process. However, with the company's revised strategy of becoming a global EPC(I) contractor, the legacy software rapidly became obsolete. A new ERP software was necessary to support HFG's emphasis on becoming a global player in engineering, procurement, construction and installation (EPC(I)) and turn-key contracting. The company needed a solution that would support its core processes, facilitate collaboration with subcontractors, and provide project management support for EPC(I) projects. The challenge was to find a solution that would meet these requirements while also being financially viable.
The Solution
After a thorough analysis of their needs and requirements, HFG selected IFS as their new ERP solution. The selection process included a workshop with an elaborate business case and scoring of the presented solutions by all project team members. IFS was chosen for its support for core processes, collaboration with subcontractors, and project management support for EPC(I) projects. After the selection, HFG started a small pilot involving all key users from the North Sea yards. The implementation began in the fall of 2007 at the Hartlepool, UK, yard and was expected to finish in 2009. One of the key success factors was involving IFS consultants in HFG's integrated project team. This approach ensured that the IFS consultants were fully committed to understanding HFG's business and delivering the desired results.
Operational Impact
Quantitative Benefit
Case Study missing?
Start adding your own!
Register with your work email and create a new case study profile for your business.
Related Case Studies.

Case Study
Taking Oil and Gas Exploration to the Next Level
DownUnder GeoSolutions (DUG) wanted to increase computing performance by 5 to 10 times to improve seismic processing. The solution must build on current architecture software investments without sacrificing existing software and scale computing without scaling IT infrastructure costs.

Case Study
Remote Wellhead Monitoring
Each wellhead was equipped with various sensors and meters that needed to be monitored and controlled from a central HMI, often miles away from the assets in the field. Redundant solar and wind generators were installed at each wellhead to support the electrical needs of the pumpstations, temperature meters, cameras, and cellular modules. In addition to asset management and remote control capabilities, data logging for remote surveillance and alarm notifications was a key demand from the customer. Terra Ferma’s solution needed to be power efficient, reliable, and capable of supporting high-bandwidth data-feeds. They needed a multi-link cellular connection to a central server that sustained reliable and redundant monitoring and control of flow meters, temperature sensors, power supply, and event-logging; including video and image files. This open-standard network needed to interface with the existing SCADA and proprietary network management software.

Case Study
System 800xA at Indian Cement Plants
Chettinad Cement recognized that further efficiencies could be achieved in its cement manufacturing process. It looked to investing in comprehensive operational and control technologies to manage and derive productivity and energy efficiency gains from the assets on Line 2, their second plant in India.

Case Study
Refinery Saves Over $700,000 with Smart Wireless
One of the largest petroleum refineries in the world is equipped to refine various types of crude oil and manufacture various grades of fuel from motor gasoline to Aviation Turbine Fuel. Due to wear and tear, eight hydrogen valves in each refinery were leaking, and each cost $1800 per ton of hydrogen vented. The plant also had leakage on nearly 30 flare control hydrocarbon valves. The refinery wanted a continuous, online monitoring system that could catch leaks early, minimize hydrogen and hydrocarbon production losses, and improve safety for maintenance.