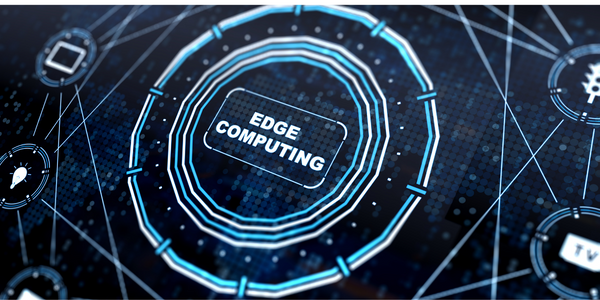
Technology Category
- Analytics & Modeling - Edge Analytics
- Analytics & Modeling - Machine Learning
- Platform as a Service (PaaS) - Edge Computing Platforms
- Processors & Edge Intelligence - Embedded & Edge Computers
Applicable Industries
- Semiconductors
Applicable Functions
- Discrete Manufacturing
Use Cases
- Edge Computing & Edge Intelligence
Services
- System Integration
The Customer
GlobalFoundries
About The Customer
A multinational semiconductor contract manufacturing and design company incorporated in the Cayman Islands and headquartered in Malta, New York.
The Challenge
Solution approach for monitoring production-critical ultrapure water valves with the aim of detecting possible failures at an early stage and better planning maintenance processes.
The Solution
Edge AI sensor platform. Features:
- Multicore: 9 RISC-V cluster cores
- 4MB RAM & 1MB MRAM
- Rich digital & analog interfaces
- CAN-FD Core
- Ethernet-TSN Core
- High Security: TRNG, OTP, AES, Secure Boot…
- Variety of supported Sensors
- Customizable Package-on-Package Peripherals
- Software SDK & Examples
Embedding AI in smart sensors.
Operational Impact
Case Study missing?
Start adding your own!
Register with your work email and create a new case study profile for your business.
Related Case Studies.
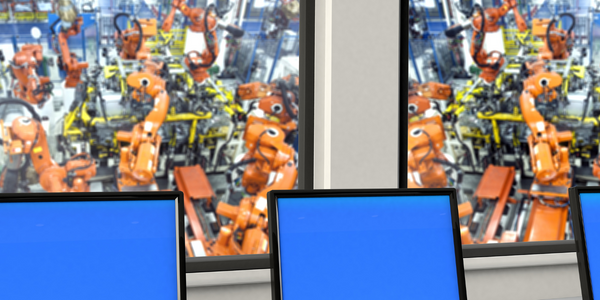
Case Study
KINESYS Semiconductor Factory Automation Software
KINESYS Software provides both Integrated Device Manufacturer (IDM) and Original Equipment Manufacturer (OEM) customers world-class software products and solutions for advanced wafer and device traceability and process management. KINESYS offers state of the art database technology with a core focus on SEMI standards. KINESYS’ challenge was to make back-end processing failure-free and easy to use for clients while supporting licensing models more adaptable to changing industry needs.
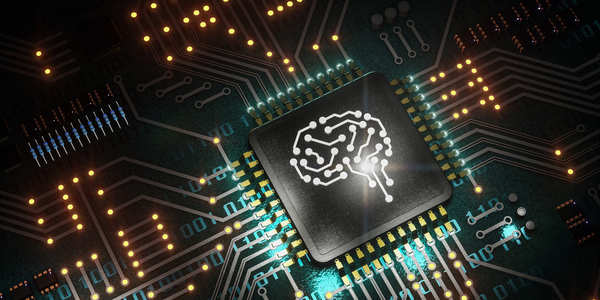
Case Study
Modular AI Defect Inspection Solution for Efficient Semiconductor Equipment Upgrades
Smasoft Technology Co., Ltd., a System Integrator that develops industrial automation software and offers AI application solutions, was commissioned by a semiconductor equipment manufacturer to implement AI inspection features into their Extreme Ultraviolet Light (EUV) pod inspection machines. The existing AOI software in the EUV pod inspection machines could only identify defective products but could not trace the cause of the defects. The manufacturer wanted to upgrade their machines with AI features to make the products more useful. The AI solution needed to complete the analysis of 380 images for a single pod within two minutes and inspect different materials simultaneously. This required multiple sets of AI models for interpretation. The solution also needed to be installed in a cabinet in the lower half of the machines, which posed a challenge due to the limited space. Smasoft needed to purchase a hardware solution with strong computing performance, stable operation, compact size, and flexible configuration to overcome these challenges.
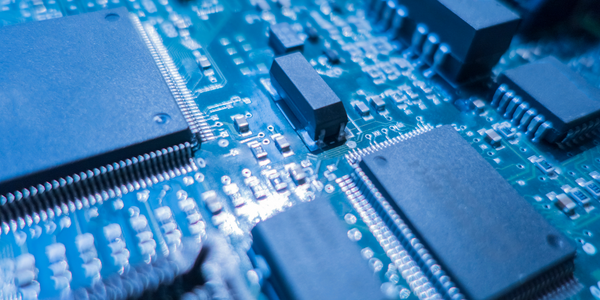
Case Study
Rapid Hybrid Services Deployment for Global Semiconductor Company
The U.S. manufacturer of engineered materials, optoelectronic components, and semiconductors was focused on growth through mergers and acquisitions (M&As). In 2019–2020, it acquired a global electronics firm and needed immediate connectivity and visibility into the acquired firm’s geo-distributed operations. The company had a highly compressed timeline, with only days to integrate the firm’s DDI operations, while deferring a full network migration to a future date. The company was actively engaged in acquiring and merging strategically aligned companies as a key global growth strategy. The company needed to rapidly integrate its new operations, which included significant remote locations in Asia. The company turned to Infoblox to quickly design a highly secure, available, and reliable solution that could deliver full visibility into new sites. It needed dynamic scalability to accommodate its growing operations and the ability to unify a disparate, geo-diverse infrastructure.
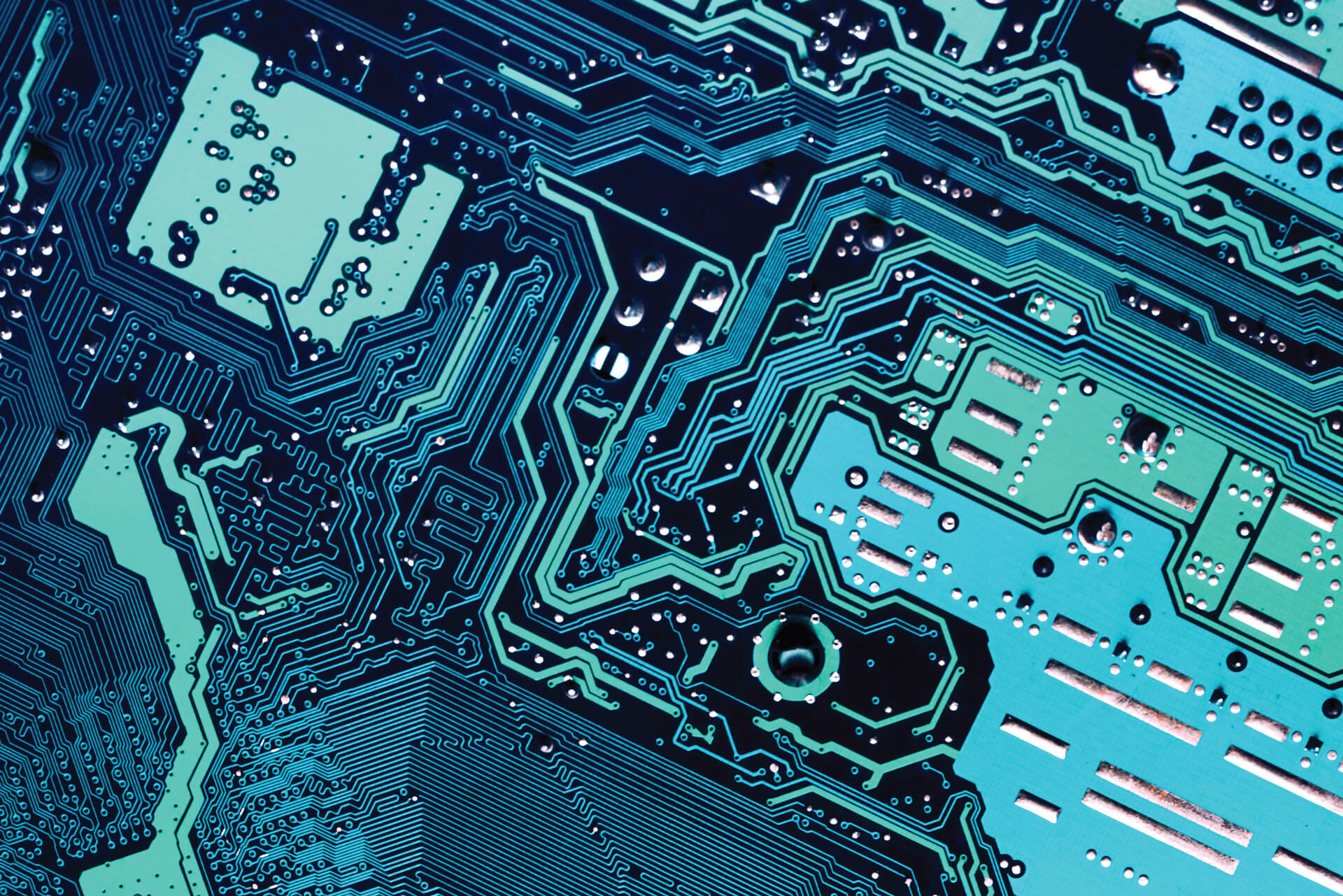
Case Study
Optimizing Semiconductor Manufacturing Yield with IoT
A large U.S.-based manufacturer of high-performance semiconductors was facing a significant challenge in optimizing the manufacturing process of its wireless products. The company, which designs and delivers a broad set of cutting-edge products including radio frequency filters, amplifiers, modulators, attenuators, and more, was experiencing lower than expected overall yield in some of its most complex products. This was affecting the company's productivity and profitability, and there was a need for a solution that could predict low-yield wafers early in the process and identify process improvements to increase overall yield.
Case Study
Leveraging Xenko Game Engine for Immersive VR Experiences: A StarBreach Case Study
Silicon Studio, the developer of the open-source cross-platform game engine Xenko, was looking to showcase the impressive graphical capabilities of their product. They aimed to demonstrate the engine's compatibility with VR and its ability to deliver high-quality virtual reality experiences and games. To achieve this, they needed to create a demo game, StarBreach, that would effectively highlight these features. However, they required an experienced art production team that could create high-quality game art for StarBreach. The challenge was not only to create visually appealing assets but also to demonstrate the technological possibilities of the Xenko game engine.
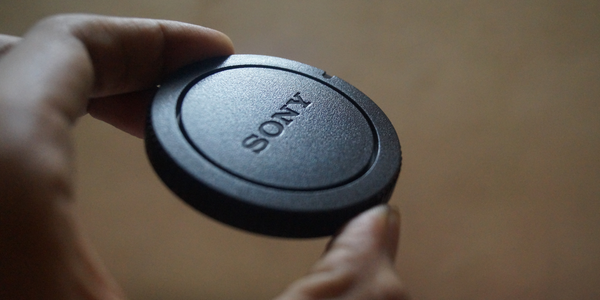
Case Study
Sony Italia's Server Consolidation: A Cost-Saving Success
Sony Italia, a branch of the global electronics giant Sony Corporation, was facing a significant challenge with its IT infrastructure. The company had consolidated most of its IT infrastructure into two data centers in the U.K, but Sony Italia opted to maintain its local server infrastructure for high performance and ease of maintenance. However, as data volumes and user numbers grew, the servers began to experience reduced performance and reliability. The company had 30 physical servers, but with limited budgets, replacing all of them was not feasible. Additionally, Sony Italia was concerned about the increasing heat output and electricity consumption in the data center. The company had already virtualized about half of its infrastructure, but needed a more cost-effective solution to extend these benefits.