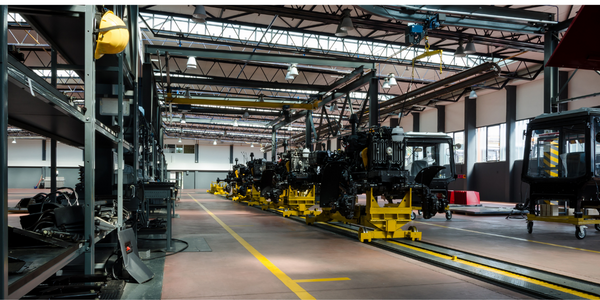
- Analytics & Modeling - Computer Vision Software
- Analytics & Modeling - Machine Learning
- Automotive
- Discrete Manufacturing
- Quality Assurance
- Computer Vision
- System Integration
In the assembly workshop of an automobile OEM, the last process of automobile production still needs to rely on a lot of manpower to assemble the body. For the scene of lamp inspection, due to the mixed production inspection, the inspectors completely rely on experience to inspect the model. In addition, due to the serious light interference on the assembly line, the inspectors also need to avoid the interference of external light sources on the detection of vehicle lights, and the detection cycle is short, which also has high requirements on the inspection speed of the inspectors.
At present, traditional manual quality inspection faces the problems of quality, special scene response and information integration:
1 Quality: In manual quality inspection, experienced quality inspectors are required to know exactly which parts are equipped with which models based on 20+ types of vehicles. The requirements for human experience are high, and new employees are unfamiliar with models. There will be problems with missed inspections.
2 In the case of a strong light source for a long time, it is necessary to take relevant human protection to prevent the eyes from being exposed to the light source for a long time.
3 Information integration: at present, it is impossible to match the material of the model and the lamp, and the material deviation cannot be traced.
The 5G+AI quality inspection solution, with the integration of AI deep visual inspection technology and 5G communication technology, automatically identifies different models based on the BOM data of the MES system.
Case Study missing?
Start adding your own!
Register with your work email and create a new case study profile for your business.
Related Case Studies.
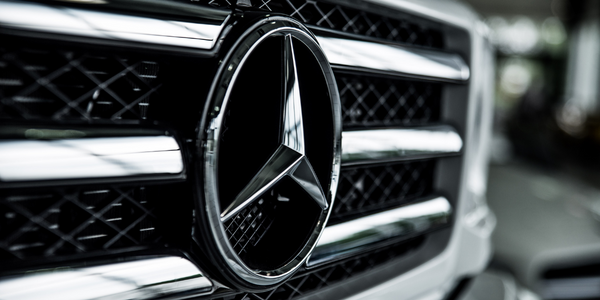
