
- Analytics & Modeling - Predictive Analytics
- Functional Applications - Remote Monitoring & Control Systems
- Sensors - Chemical Sensors
- Chemicals
- Maintenance
- Predictive Maintenance
At the corporation’s Mizushima plant near Okayama, pH measurement during the neutralization of strong acids is closely monitored. For this important measurement Tsutomu Ishikawa and Naoto Ogura, engineers at the plant’s Instrumentation and Engineering Department were not satisfied with the performance of the pH sensors they were using.
For this reason, sensors were regularly exchanged at the plant to minimize the chance of failure in the process. But the operation cost was high and Mr. Ishikawa and Mr. Ogura needed a better solution. Specifically, they required to know in advance when a pH sensor would need to be cleaned, calibrated or replaced: “We wanted to grasp how deposits forming on the pH sensors would affect the timing of sensor maintenance and exchange.”
Intelligent Sensor Management (ISM®) provides exactly this ability. By continuously monitoring process conditions, sensor slope and reference system impedance value ISM pH sensors can predict their remaining lifetime and when calibration and cleaning should be performed. Further, ISM’s predictive diagnostic tools (displayed on the connected transmitter) are dynamic, so as process and sensor conditions change, the diagnostics readjust.
To test ISM at the facility, two pH measurement systems comprising InPro® 4260i sensors and M400 transmitters were installed on neutralization equipment. The METTLER TOLEDO solutions functioned extremely well and further ISM pH systems were installed for monitoring organic solvents.
Case Study missing?
Start adding your own!
Register with your work email and create a new case study profile for your business.
Related Case Studies.
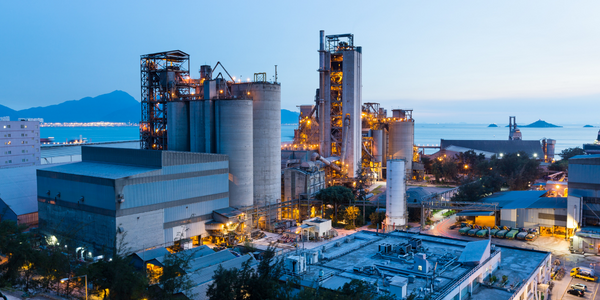
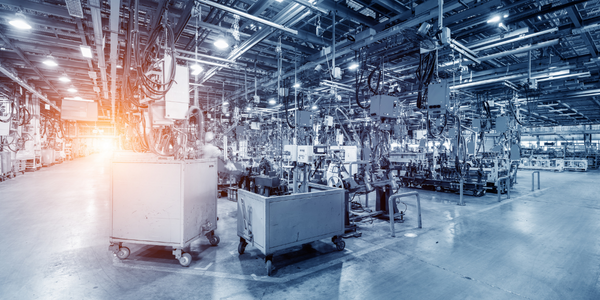
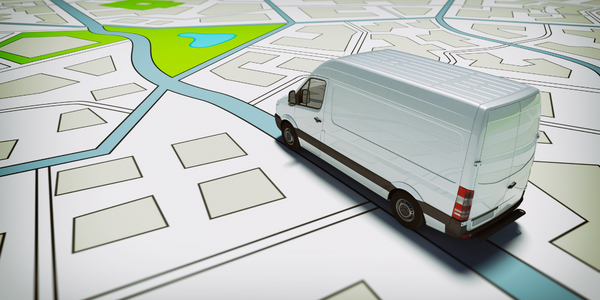
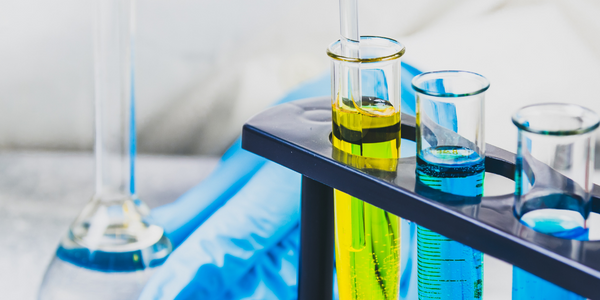
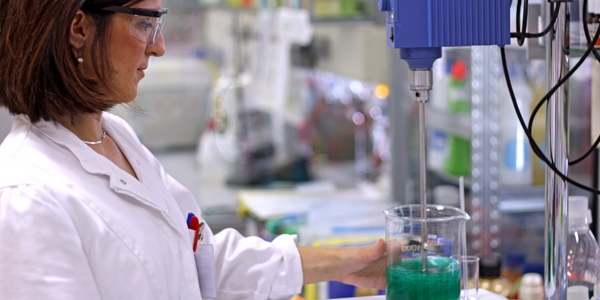