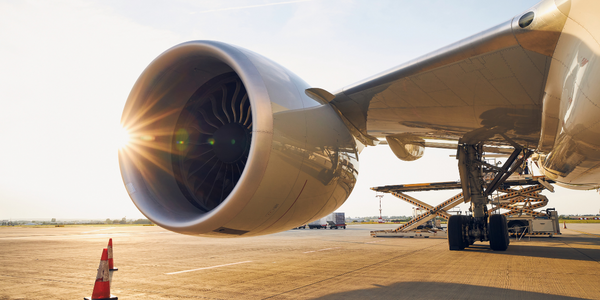
Technology Category
- Application Infrastructure & Middleware - Middleware, SDKs & Libraries
- Functional Applications - Manufacturing Execution Systems (MES)
Applicable Industries
- Aerospace
- Equipment & Machinery
Applicable Functions
- Human Resources
- Quality Assurance
Use Cases
- Additive Manufacturing
- Manufacturing Process Simulation
Services
- System Integration
The Customer
Acatec S.L.
About The Customer
Acatec S.L. is a leading manufacturer of precision aeronautical components based in Spain. The company is known for its innovative production process, which has propelled it into the vanguard of the European aeronautical manufacturing industry. As a quality-focused enterprise, Acatec is a high-demand, low-cost provider to renowned aerospace companies such as Airbus, EADS Casa, and Composite International SA. The company is committed to reducing costs and outperforming client expectations by embracing new technologies. This commitment led them to overhaul their entire process, from the purchase of raw materials to the final delivery of the product.
The Challenge
Acatec S.L., a leading manufacturer of precision aeronautical components based in Spain, was striving to reduce costs and exceed client expectations by embracing new technologies. The company decided to overhaul its entire process, from the purchase of raw materials to the final delivery of the product. However, Acatec had historically outsourced all macro engineering and IT/Technology projects to external professional service companies. This resulted in a lack of in-house engineering and technology personnel to drive productivity improvement initiatives. To improve productivity, Acatec decided to implement time-saving, resource-light systems aimed at assisting forward planning of work, gauging capacities, and managing demanding delivery schedules. This included the implementation of management systems for warehouses and computerized control productions. However, the company soon realized that the first step towards increased productivity and efficiency was measuring the actual events.
The Solution
The lean team at Acatec understood the value of consistent, reliable data in the form of metrics, such as Overall Equipment Effectiveness (OEE). They assessed that Acatec needed a technology vendor that would provide a turnkey system and installation of the equipment, along with interpretation of the data, making adoption relatively simple in regards to Continuous Improvement. After a thorough needs assessment and selection process, Acatec decided on deploying the MERLIN communications platform utilizing the MERLIN Ax9150 Universal Machine Interface MTConnect adapter for automated data collection and Handheld HMI for downtime recording. The company started a pilot project at its Madrid plant with two machines in May of 2011. The results were so compelling that management deemed it a success within four weeks and proceeded to roll out a full plant-wide installation throughout the Madrid facility. Acatec installed the MERLIN software and hardware adapters in August 2011 and then gathered benchmark data in September 2011. The manufacturing team then made procedural changes to their processes through October to December 2011.
Operational Impact
Quantitative Benefit
Case Study missing?
Start adding your own!
Register with your work email and create a new case study profile for your business.
Related Case Studies.

Case Study
Smart Water Filtration Systems
Before working with Ayla Networks, Ozner was already using cloud connectivity to identify and solve water-filtration system malfunctions as well as to monitor filter cartridges for replacements.But, in June 2015, Ozner executives talked with Ayla about how the company might further improve its water systems with IoT technology. They liked what they heard from Ayla, but the executives needed to be sure that Ayla’s Agile IoT Platform provided the security and reliability Ozner required.

Case Study
IoT enabled Fleet Management with MindSphere
In view of growing competition, Gämmerler had a strong need to remain competitive via process optimization, reliability and gentle handling of printed products, even at highest press speeds. In addition, a digitalization initiative also included developing a key differentiation via data-driven services offers.
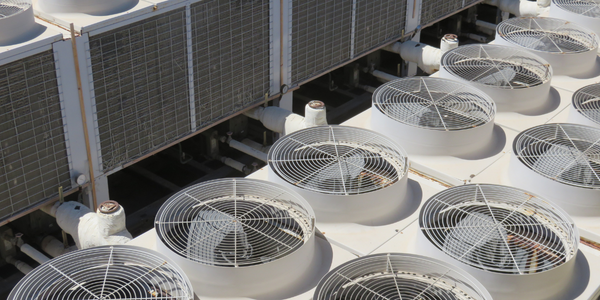
Case Study
Predictive Maintenance for Industrial Chillers
For global leaders in the industrial chiller manufacturing, reliability of the entire production process is of the utmost importance. Chillers are refrigeration systems that produce ice water to provide cooling for a process or industrial application. One of those leaders sought a way to respond to asset performance issues, even before they occur. The intelligence to guarantee maximum reliability of cooling devices is embedded (pre-alarming). A pre-alarming phase means that the cooling device still works, but symptoms may appear, telling manufacturers that a failure is likely to occur in the near future. Chillers who are not internet connected at that moment, provide little insight in this pre-alarming phase.

Case Study
Premium Appliance Producer Innovates with Internet of Everything
Sub-Zero faced the largest product launch in the company’s history:It wanted to launch 60 new products as scheduled while simultaneously opening a new “greenfield” production facility, yet still adhering to stringent quality requirements and manage issues from new supply-chain partners. A the same time, it wanted to increase staff productivity time and collaboration while reducing travel and costs.

Case Study
Integration of PLC with IoT for Bosch Rexroth
The application arises from the need to monitor and anticipate the problems of one or more machines managed by a PLC. These problems, often resulting from the accumulation over time of small discrepancies, require, when they occur, ex post technical operations maintenance.
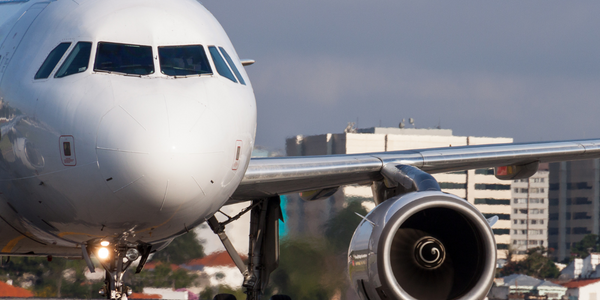
Case Study
Airbus Soars with Wearable Technology
Building an Airbus aircraft involves complex manufacturing processes consisting of thousands of moving parts. Speed and accuracy are critical to business and competitive advantage. Improvements in both would have high impact on Airbus’ bottom line. Airbus wanted to help operators reduce the complexity of assembling cabin seats and decrease the time required to complete this task.