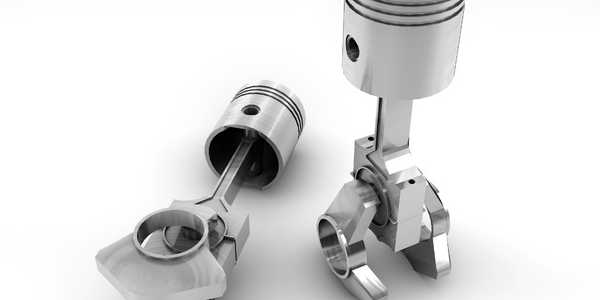
- Analytics & Modeling - Computer Vision Software
- Sensors - Camera / Video Systems
- Equipment & Machinery
- Quality Assurance
- Visual Quality Detection
Earth moving machines require an immense energy source to provide the power they need for use within civil engineering works. ‘Hydraulic Motors’ allow this power to be applied to enable the machines movement and in addition ‘Control Valves’ also provide the operator with the precise feel and control required to undertake the necessary tasks needed for such machines, including trenching, rock breaking and demolition. These same motors are also used in cranes, wheel loaders and general construction equipment. Though not a new product, the designs of such motors and control valves have been around a few decades, the overall method for manufacture has changed rapidly over the last few years to take account of the need for more modular designs, manufacture and just-in-time manufacturing. Kawasaki Precision Machinery (UK) Ltd based in Plymouth, UK is one of the leading manufacturers of such motors and pumps. They approached Industrial Vision Systems Ltd to come up with a solution to provide automated inspection of such pumps for their semi-automated assembly process. The pumps requiring inspection are at a sub-assembly stage when they are due for the inspection process to take place. Due to the highly modular nature of the construction each part of the pump can have many different derivatives which overall have a different effect on the pump in industrial use. It is therefore critical for the manufacturing process to check all components are the correct type and number for the construction of the pump to begin. Once built it is difficult and costly to rework such units if a fault is detected later in the manufacturing process, therefore automated visual inspection is critical for the success in building quality motors and pumps.
The first part of the project involved systematically defining how each part could be presented on a fixture to the vision system, ideally fitting all components onto one large fixture design in order for multiple cameras to view all components in one inspection position. Once the final design for the travel board fixture was defined the final camera position and lighting position could be confirmed. The machine incorporates a central roller feed conveyor system and incorporated into the conveyor are pneumatically-driven stops. The cameras, optics and lights are mounted from individual doweled fixtures mounted inside the main inspection canopy. The whole system was shielded from ambient lighting to stop this affecting the vision system result. Machine vision inspection functions were then selected from standard routines available in the IVS software and deployed to check the six main components on the fixture board in sequence. The main pump inspection and the associated valve plate and cover checks were completed via the use of a match against a trained template of the relevant type. Due to the precise positioning of the products on the board no rotational movement of the templates was required. After the software has examined all the characteristics of all the components, it then determines whether the pump manifest meets all the tolerances that have been specified, or whether the parts must be reworked or rejected.
Case Study missing?
Start adding your own!
Register with your work email and create a new case study profile for your business.
Related Case Studies.


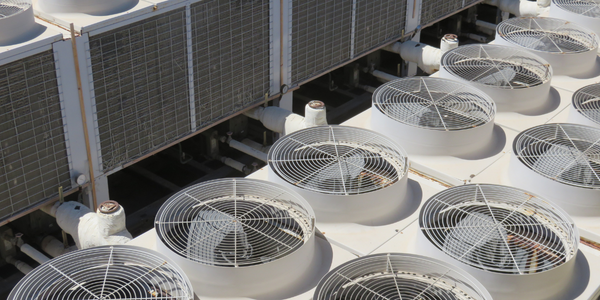


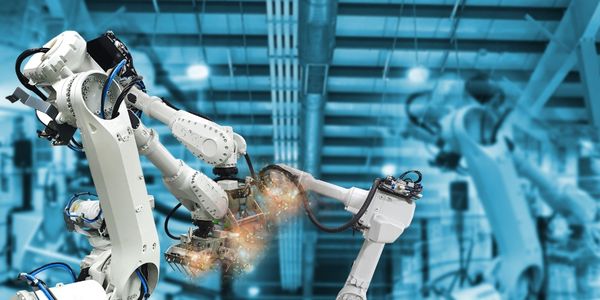