Aircraft component manufacturer introduces predictive maintenance

- Analytics & Modeling - Machine Learning
- Analytics & Modeling - Predictive Analytics
- Networks & Connectivity - Gateways
- Aerospace
- Maintenance
- Predictive Maintenance
A major European aircraft component supplier encountered this challenge first-hand. A mission-critical, programmable milling machine failed, halting the organization’s production process. Despite the customer team’s expertise, the problem proved challenging to diagnose. At first, it appeared the downtime resulted from a damaged spindle, the most complicated part of the milling machine. However, a costly and time-consuming spindle replacement did not correct the situation. The team was forced to perform an extensive system evaluation to identify the culprit.
The solution features multiple, integrated elements. By incorporating numerous XIoT devices and other monitoring applications alongside the milling machines, the maintenance solution can take a holistic view of the tools it oversees and identify the baseline characteristics for “normal” system operation. While milling machines remain within normal parameters, the system takes no action. However, should the monitoring system detect a deviation from the norm – such as changes in temperature, energy consumption, the number of spindle turns per second, or load on the spindle – its built-in analysis capability can automatically identify an appropriate course of action. Capgemini’s solution can then alert and dispatch repair personnel, or send messages to alternate staff depending on the severity of the scenario.
Case Study missing?
Start adding your own!
Register with your work email and create a new case study profile for your business.
Related Case Studies.
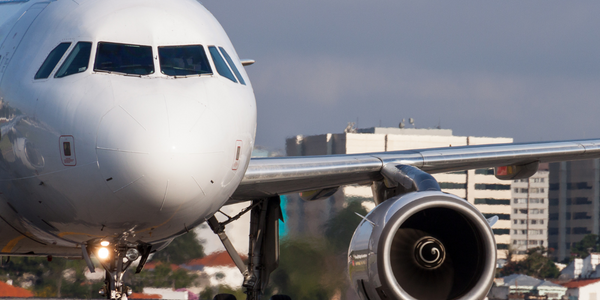
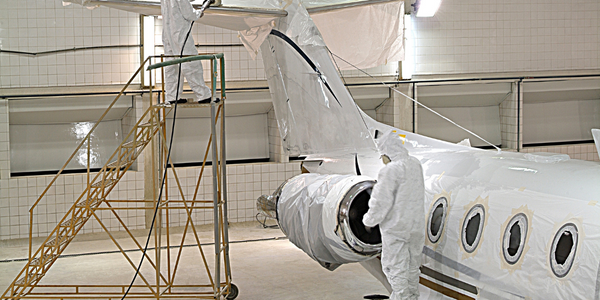
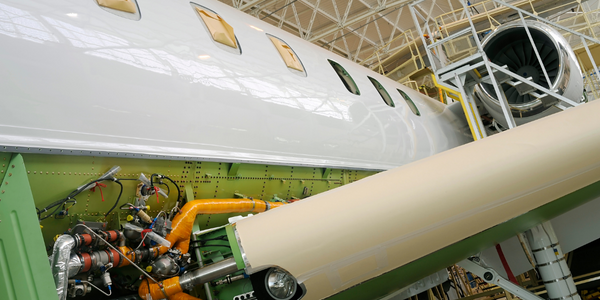
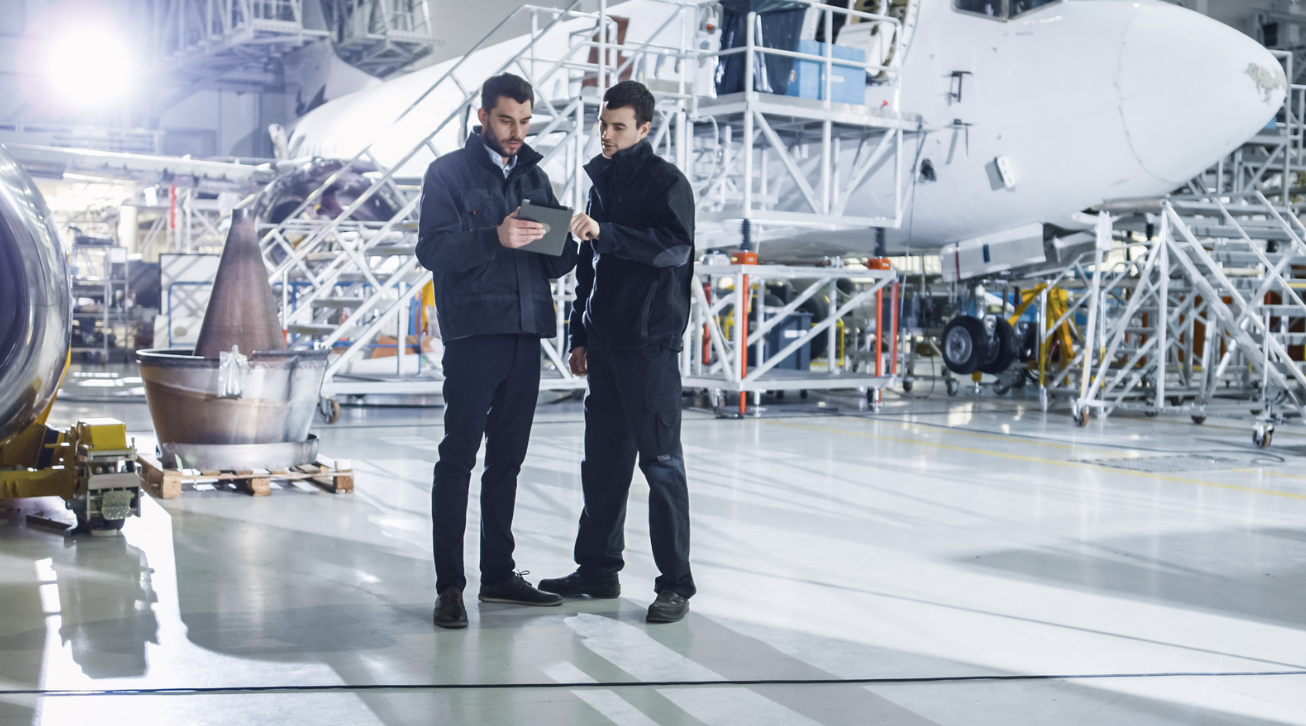
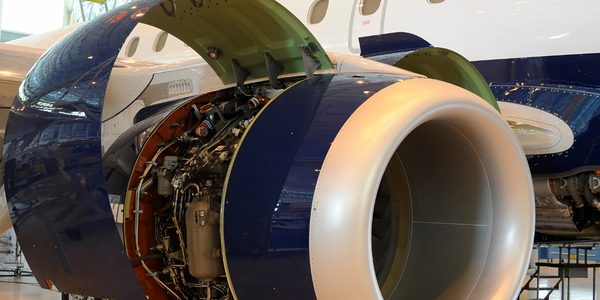