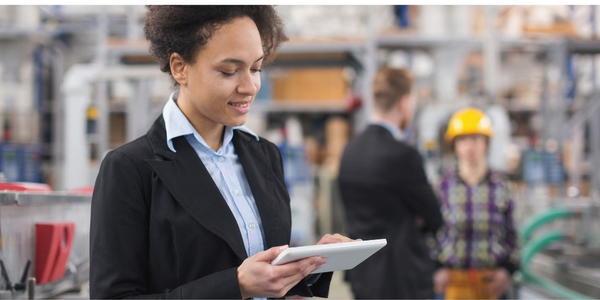
- Analytics & Modeling - Computer Vision Software
- Analytics & Modeling - Machine Learning
- Electronics
- Discrete Manufacturing
- Quality Assurance
- Computer Vision
- Visual Quality Detection
- System Integration
For a 3C product supply chain enterprise, the monthly labour cost of manual visual inspection exceeds 2 million, the proportion of quality inspection personnel accounts for 20%~40%, and there are quality problems such as missed inspections. At present, manual quality inspection is faced with the problems of quality, cost, response to special scenarios, and information integration. The details are as follows:
- Quality: The subjective factor of manual quality inspection has a great influence on the judgment result, and there will be a problem of missed inspection based on visual fatigue; Production status of a 3C product supply chain enterprise.
- Information integration: There is no effective accumulation and utilization of production data, and subsequent process reengineering and quality analysis cannot be promoted, and the adaptation to automated production processes is weak.
- Cost: The turnover of personnel is high, resulting in high training and labour costs, and it is difficult to recruit workers.
- Efficiency: Traditional machine vision uses programmed computing logic for visual inspection, which has poor anti-interference ability for such complex surface inspection, high false detection, and heavy workload for personnel re-judgment.
The 5G+AI appearance quality inspection scheme, with the integration of AI depth visual inspection technology and 5G communication technology.
Case Study missing?
Start adding your own!
Register with your work email and create a new case study profile for your business.
Related Case Studies.

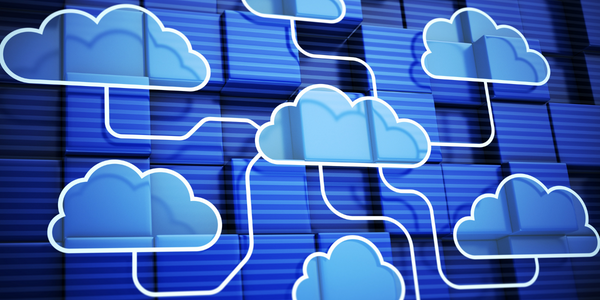
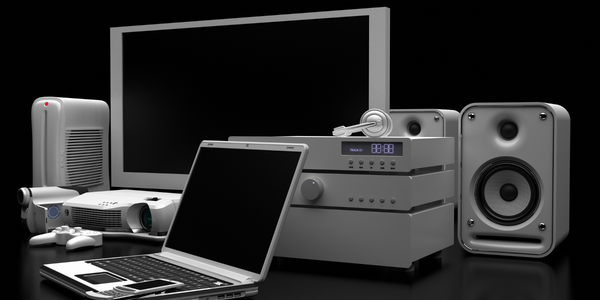